Summary:
Choosing the Best Mobile Port Loader: Key Considerations
Factors to Consider When Choosing a Mobile Port Loader
Evaluating Operational Costs and Maintenance Requirements
Technology and Innovation in Mobile Port Loaders
Choosing the Best Mobile Port Loader for Your Specific Needs
Factors to Consider When Choosing a Mobile Port Loader
When choosing a mobile port loader, several key factors should be carefully considered to ensure it meets the operational requirements of your port. Here are the factors to keep in mind:
Performance and Efficiency
Lifting Capacity: Assess the loader’s maximum lifting capacity to ensure it can handle the weight of typical containers or cargo at your port without compromising efficiency or safety.
Speed and Productivity: Evaluate the loader’s operational speed and productivity metrics such as cycles per hour or containers moved per hour. This helps gauge its efficiency in handling peak operational demands.
Fuel Efficiency: Consider the loader’s fuel consumption rate per hour of operation. Opting for models with higher fuel efficiency can lead to significant cost savings over time.
Safety Features and Compliance
Safety Standards: Ensure the loader meets all relevant safety standards and regulations. Look for features such as anti-collision systems, load monitoring sensors, and ergonomic design to enhance safety for operators and minimize the risk of accidents.
Operator Training and Support: Evaluate the availability of comprehensive training programs for operators. Well-trained personnel are crucial for safe and efficient operation of the loader.
Environmental Compliance: Check if the loader complies with environmental regulations regarding emissions, noise levels, and fuel usage. Opting for environmentally friendly models can align with sustainability goals.
Adaptability to Various Port Environments
Terrain Compatibility: Consider the terrain where the loader will operate (e.g., paved surfaces, uneven ground). Choose a loader with appropriate tires or tracks for optimal traction and maneuverability.
Weather Resistance: Evaluate the loader’s ability to operate effectively in various weather conditions prevalent in your port area (e.g., rain, extreme temperatures). Weather-resistant features can ensure continuous operation without interruptions.
Maintenance Requirements: Assess the loader’s maintenance needs, including frequency of servicing, availability of spare parts, and ease of maintenance procedures. Minimizing downtime due to maintenance is crucial for maintaining operational efficiency.
Choosing the best mobile port loader involves weighing these factors against your specific operational needs and budget constraints. By prioritizing performance, safety, adaptability, and maintenance considerations, you can select a loader that enhances productivity and efficiency in your port operations while ensuring compliance with regulatory requirements.
Evaluating Operational Costs and Maintenance Requirements
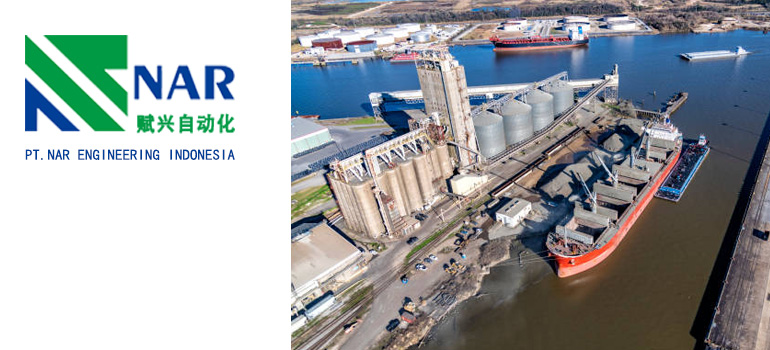
When evaluating operational costs and maintenance requirements for a mobile port loader, it’s essential to consider several key aspects to ensure long-term efficiency and cost-effectiveness. Here’s a detailed exploration:
Cost Considerations in Acquisition
Initial Investment: Compare the upfront costs of different models based on their specifications and capabilities. Opt for a loader that balances initial investment with long-term operational benefits.
Total Cost of Ownership (TCO): Calculate the TCO over the expected lifespan of the loader, considering factors such as fuel consumption, maintenance costs, depreciation, and resale value. A lower TCO indicates better cost-efficiency.
Financing Options: Explore financing options available for purchasing the loader, such as leasing, loans, or outright purchase. Consider the impact of financing on overall costs and cash flow.
Long-term Maintenance Planning
Maintenance Schedule: Review the manufacturer’s recommended maintenance schedule for the loader. Regular servicing and inspections help prevent breakdowns and extend the equipment’s lifespan.
Spare Parts Availability: Check the availability of spare parts for the loader. Opt for models with readily accessible parts to minimize downtime and operational disruptions.
Service Provider Accessibility: Assess the availability of qualified service providers or technicians capable of servicing the loader in your port area. Prompt service response can reduce downtime and operational losses.
Return on Investment Considerations
Operational Efficiency: Evaluate how the loader’s performance and features contribute to operational efficiency, such as handling capacity, speed, and fuel efficiency. Higher efficiency often translates into better ROI.
Revenue Generation: Consider how the loader contributes to revenue generation by increasing throughput or handling capacity. Compare potential revenue gains against operational costs to assess ROI.
Resale Value: Estimate the loader’s resale value at the end of its useful life. Choosing a model with good resale potential can mitigate initial acquisition costs.
Evaluating operational costs and maintenance requirements involves a comprehensive analysis of acquisition costs, ongoing maintenance needs, and potential returns on investment. By prioritizing cost-efficiency, long-term maintenance planning, and ROI considerations, you can select a mobile port loader that aligns with your port’s operational goals while maximizing financial benefits over its lifespan.
Technology and Innovation in Mobile Port Loaders
Technology and innovation play pivotal roles in the evolution of mobile port loaders, enhancing their efficiency, safety, and environmental sustainability. Here’s an exploration of how advancements in technology are shaping the landscape of mobile port loaders:
Integration of Smart Technologies
Automated Systems: Discuss the integration of automated systems in modern mobile port loaders, such as automated stacking cranes (ASCs) or automated guided vehicles (AGVs). These systems optimize container handling processes, reducing human error and improving operational efficiency.
Telematics and IoT: Explain how telematics and Internet of Things (IoT) technologies are used to monitor loader performance in real-time. Data on fuel consumption, engine health, and operational metrics can be remotely accessed and analyzed, enabling proactive maintenance and operational adjustments.
Advanced Control Systems: Highlight advancements in control systems, including joystick controls with haptic feedback and ergonomic design. These innovations enhance operator comfort and precision during loading and unloading operations.
Impact of Automation and Robotics
Remote Operation and Telepresence: Discuss the use of remote operation and telepresence technologies, allowing operators to control loaders from a safe distance. This capability enhances safety in hazardous environments while maintaining operational efficiency.
Robotics in Maintenance: Explore how robotics and drones are used for maintenance tasks such as inspection, cleaning, and minor repairs. Automated maintenance procedures reduce downtime and improve overall equipment reliability.
AI and Machine Learning: Explain the application of artificial intelligence (AI) and machine learning algorithms in predictive maintenance and operational planning. These technologies analyze historical data to predict equipment failures, optimize maintenance schedules, and enhance performance.
Sustainability and Environmental Considerations
Emission Reduction Technologies: Describe advancements in emission reduction technologies, such as hybrid engines, electric-powered loaders, and exhaust gas treatment systems. These innovations minimize environmental impact and align with sustainability goals.
Energy Efficiency: Discuss initiatives to improve energy efficiency through regenerative braking systems, idle reduction technologies, and optimized engine designs. Energy-efficient loaders reduce fuel consumption and operating costs while lowering carbon footprint.
Material Recycling and Lifecycle Management: Highlight efforts to incorporate recycled materials in loader construction and improve end-of-life recycling processes. Sustainable lifecycle management practices reduce resource consumption and waste generation.
Technology and innovation continue to drive significant advancements in mobile port loaders, enhancing their capabilities in efficiency, safety, and environmental sustainability. By embracing smart technologies, automation, and sustainable practices, port operators can optimize operations, reduce costs, and mitigate environmental impact, ensuring long-term competitiveness and compliance with regulatory standards.
Choosing the Best Mobile Port Loader for Your Specific Needs
Choosing the best mobile port loader tailored to your specific operational needs requires careful consideration of several key factors. Here’s a comprehensive guide to help you make an informed decision:
Matching Loader Capacities to Requirements
Container Handling Capacity: Assess the loader’s lifting capacity to ensure it can efficiently handle the weight and size of containers typically processed at your port. Consider variations in container sizes (20-foot, 40-foot, etc.) that your operations frequently handle.
Stacking Height and Reach: Evaluate the loader’s stacking height capabilities and horizontal reach. Ensure it can stack containers safely and effectively within the designated storage areas of your port facility.
Versatility in Cargo Handling: Consider if the loader can handle other types of cargo besides containers, such as bulk materials or heavy machinery. Versatile loaders add flexibility to your operations.
Customization Options and Flexibility
Adaptability to Port Environment: Assess how well the loader adapts to the specific terrain and operational conditions of your port. Factors to consider include ground conditions, weather resilience, and maneuverability in tight spaces.
Attachments and Accessories: Evaluate the availability of compatible attachments or accessories (e.g., spreaders, lifting beams) that enhance the loader’s versatility and efficiency in handling different types of cargo.
Customizable Features: Check if the loader offers customizable features or configurations to meet unique operational requirements. Customization options may include cabin layouts, control systems, and ergonomic enhancements for operator comfort.
Case Studies and Success Stories
Industry Performance and Reliability: Research case studies or success stories of similar ports or logistics companies using the loader models you are considering. Learn from their experiences with reliability, uptime, and overall satisfaction.
User Feedback and Reviews: Seek feedback from operators or maintenance personnel who have hands-on experience with the loaders. User reviews can provide valuable insights into performance, ease of maintenance, and service support.
Long-term Support and Service: Evaluate the manufacturer’s reputation for customer support, spare parts availability, and service network. A reliable support system ensures prompt assistance in case of maintenance issues or technical challenges.
Choosing the best mobile port loader involves a thorough assessment of its capabilities, customization options, and compatibility with your port’s operational environment. By aligning loader capacities with your specific handling requirements, exploring customization opportunities, and leveraging insights from industry peers, you can select a loader that enhances efficiency, flexibility, and overall operational performance in your port operations.